Participation of INCAS at the Official Presentation of the European RACER Demonstrator, as the coordinator of the RoRCraft Consortium
On May 15th, 2024, the official presentation of the RACER Demonstrator took place, organized by Airbus Helicopters in Marignane, France. The flight of the RACER helicopter marked a crucial milestone for the European Commission's Clean Aviation technology initiative as well as for the involved partners.
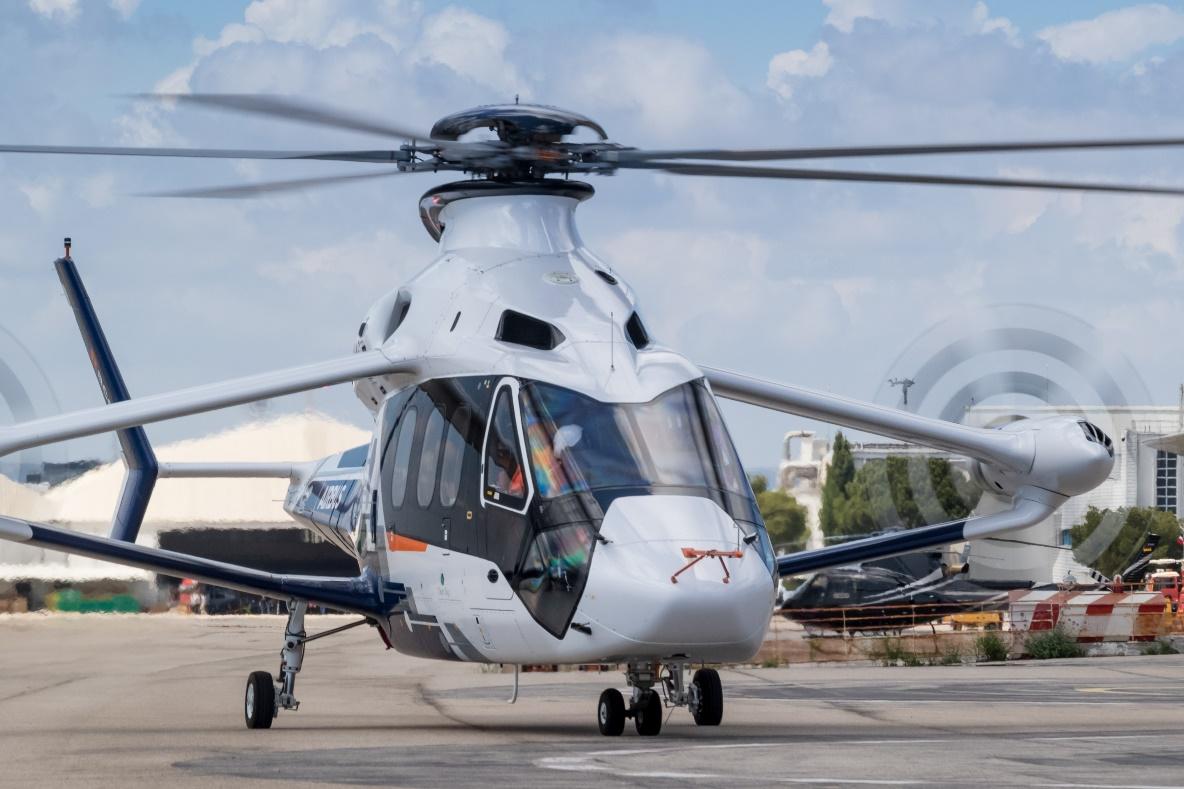
The RACER Demonstrator is the result of a robust European collaborative research program, developed under the coordination of Airbus Helicopters along with 40 partners from 13 European countries, including Romania, through the RoRCraft consortium formed by INCAS – National Institute for Aerospace Research “Elie Carafoli” and ROMAERO S.A.
With a cruise speed reaching 400 Km/h, RACER is a helicopter demonstrator aimed at reducing costs by 25% per nautical mile compared to a conventional helicopter, as well as reducing fuel consumption and noise by approximately 20% for typical passenger transport missions. This innovation demonstrates a commitment to revolutionizing helicopter technology to achieve tangible environmental benefits for society.
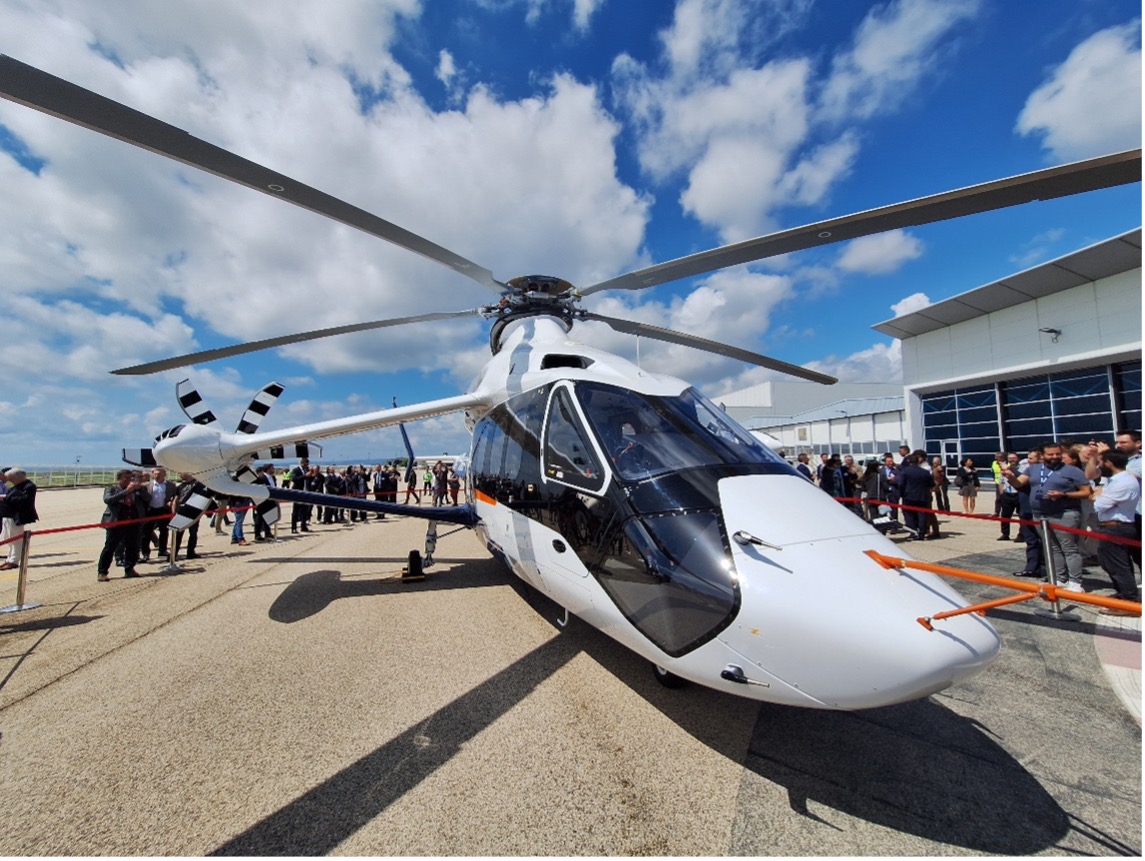
The activities of the Romanian consortium RoRCraft, coordinated by INCAS – National Institute for Aerospace Research “Elie Carafoli” within the European partnership, involved the design, manufacturing, testing, and development of certification documentation for the Main Fuselage of the future helicopter. INCAS, as the consortium leader, demonstrated even before winning the project that it has the experience to approach a project of such magnitude (TRL 6) multi-systemically, and is also capable of leading production and testing activities, aspects that are vital to the success of such a European initiative. The trust placed in INCAS by Airbus Helicopters, the coordinator of the RACER program, was reflected in the allocation of a significant portion of the helicopter with a high degree of technological risk.
As part of the project, INCAS performed advanced design activities in the field of metallic and composite structures, using the latest technologies in the field, such as Virtual and Augmented Reality, to optimize maintenance activities. The design team integrated all interfaces corresponding to the helicopter systems (more than 360 interfaces) into the fuselage structure, some of which are critical from an architectural standpoint. The technologies proposed for the fuselage construction (hybrid metal-composite structure, use of additive manufacturing in structural parts etc.) and the strength calculation methods used led to the achievement of an optimal structure in terms of load-bearing capability relative to the structure’s weight.
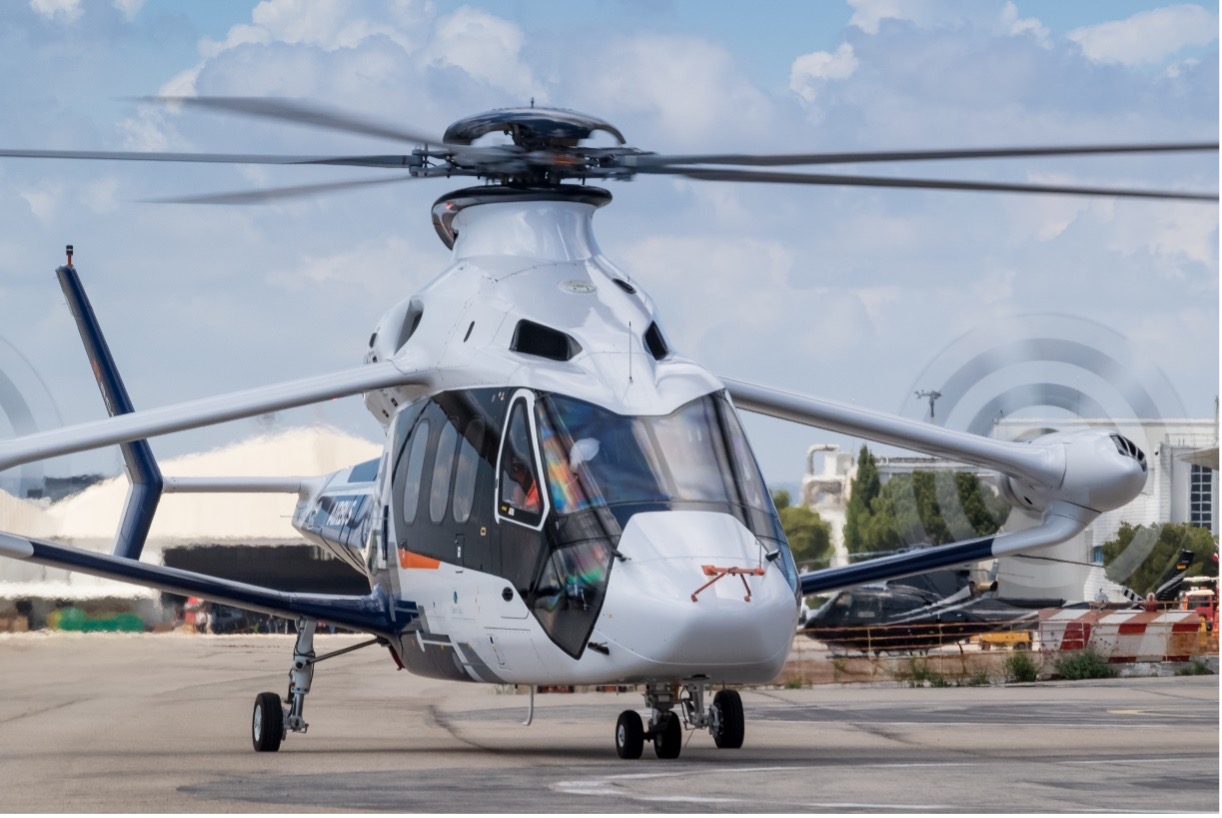
INCAS coordinated the manufacturing activities for the Main Fuselage and the specimens intended for the tests required for certification. This involved internally organizing the fuselage structure and optimizing the process of delivering the execution documentation to the partner ROMAERO, thereby creating a conducive environment for manufacturing activities (minimizing risks related to the acquisition of materials, tools and standardized parts) by improving the infrastructure allocated to manufacturing and supporting manufacturing activities during the COVID-19 pandemic.
The static strength testing activities for the two large specimens from the Main Fuselage area were carried out at STRAERO, an aviation structure testing entity that is part of the INCAS Group. The tests, based on the test orders developed by the INCAS strength calculation team, involved applying a complex system of forces at the fuselage’s junction interfaces with other structural elements (such as wings, landing gear etc.) and measuring their effects on the structure. Through the professionalism of the testing specialists, they developed a unique testing ecosystem in Romania, which ensured not only the successful execution of all loading cases but also provided a high degree of safety in protecting these unique specimens from potential damage due to the large forces applied (on the order of tons).
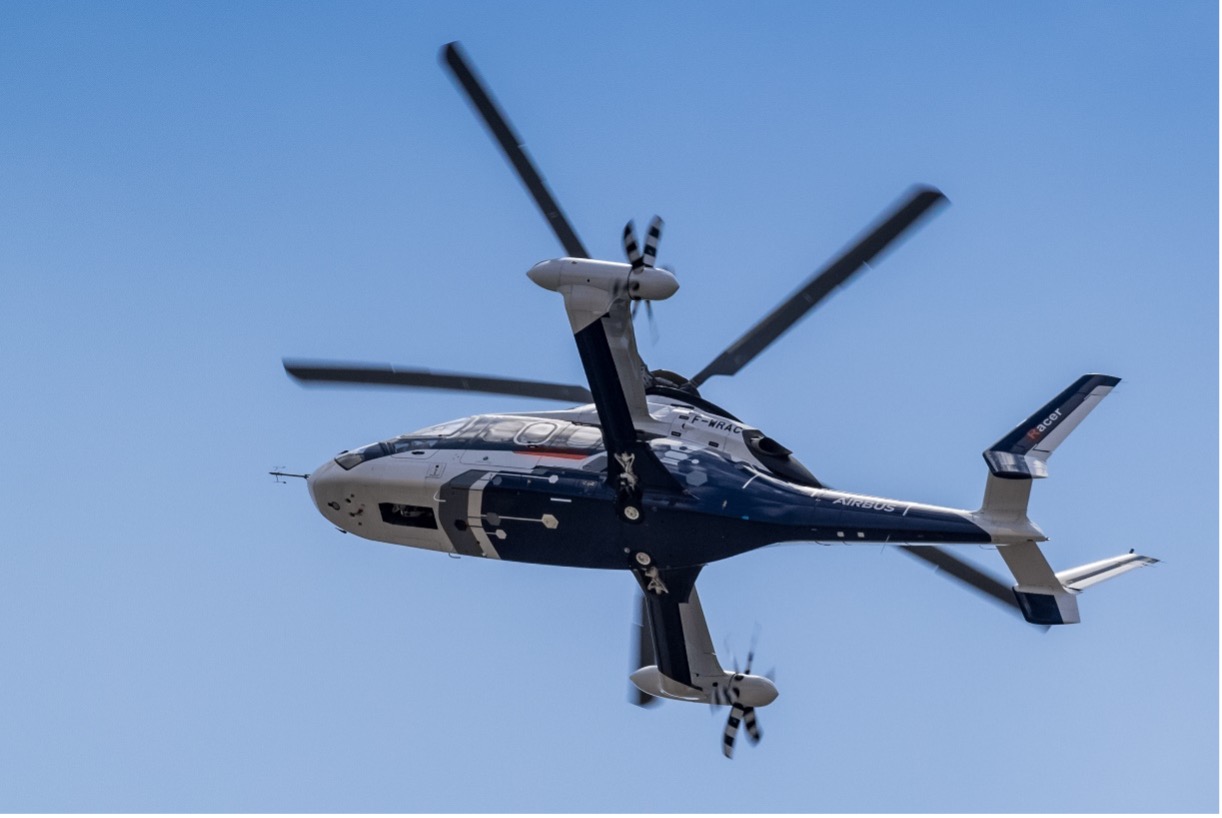
The stress documentation developed by the specialists at INCAS formed the basis for the entire helicopter’s certification activities before the French Aviation Authority to obtain the Permit-to-Fly. The complex structural calculation methods were validated through the physical tests performed on the static test specimens according to the testing pyramid and were applied to substantiate the structural behaviour. By Airbus Helicopters accepting the substantiation philosophy proposed by INCAS and the completion and submission of the stress documentation, the Institute demonstrated its capability to successfully undertake certification activities in the aeronautical field in accordance with current EASA regulations.