RoRCraft
Rotorcraft (sometimes referred to as rotary wing aircraft) are aircraft that use lift generated by rotors - these are assemblies comprising several rotor blades that revolve around a mast. Rotorcraft generally have one or more rotors to provide lift throughout the entire flight, and while a helicopter is a type of rotorcraft, not all rotorcraft are helicopters.
For more information, please visit the official project page website
Clean Sky 2 Joint Undertaking: CS2 –FRC-GAM -2014-2015-01
Acronym Project: RoRCraft
Project duration (months): 66 months
Starting date project: July 1, 2015
Ending date project: December 31, 2020
Project Coordinator:
The Clean Sky 2 Joint Undertaking (the “JU“), represented by Executive Director, Eric Dautriat, of the one part, Airbus Helicopters, represented by Guillaume Faury, Chief Executive Officer (coordinator), (Beneficiary no 1)
Adress:
Official registration number: 352383715 established in Aeroport International Marseille-Provence, 13725 Marignane Cedex, France
Project Presentation
The main objective of INCAS, within the PNCDI III project, Subprogram 3.6 – Rewarding participation in Horizon 2020, is to provide scientific and technical support for the European Project RotorCraft Fuselage Manufacturing for LifeRCraft Demonstrator – RoRCraft, in which ROC – the Romanian Cluster coordinated by INCAS, aims at designing, manufacturing, testing and permit to fly support for the fuselage of LifeRCraft Compound Rotorcraft Demonstrator.
The RoRCraft project is part of a European partnership created within Clean Sky 2 Fast Rotorcraft IADP Program to develop a new technological demonstrator named LifeRCraft Compound Rotorcraft Demonstrator under AIRBUS Helicopters leadership.
The LifeRCraft project aims to develop new capabilities for a new helicopter configuration by implementing and integrating cutting-edge technologies developed within Clean Sky 1 Program, providing both operators and industry new mobility options that neither conventional helicopters nor fixed wing aircraft can currently cover in a sustainable way.
The project is based on:
– Identified mobility requirements and environmental protection objectives;
– Lessons learnt from earlier experimentation with the X3 low scale exploratory aircraft;
– Technology progress achieved for rotorcraft subsystems on one side through participation in Clean Sky projects and other research activities at EU or local level.
The Clean Sky 2 goal is to identify, develop and validate the key technologies necessary to achieve major steps towards the ACARE (Advisory Council for Aviation Research and Innovation in Europe) environmental goals for 2020. The main target is to substantially contribute to fuel consumption and carbon dioxide (CO2) emissions reduced by 50%, Nitrous oxides (NOX) emissions reduced by 80%, reduction in perceived external noise of 50%. Another goal is to improve the environmental impact of the life cycle of aeronautical products (manufacturing, operation, maintenance and disposal).
Taking into account the increasing of the rotorcraft European production market share, technology is a key factor which sustaining this trend.
This consortium builds on the already successful participation of the INCAS Cluster in Clean Sky 1 activities, mainly for SFWA ITD where they are in charge with a significant part of the design and manufacturing activities in BLADE demonstrator, the largest in-flight demonstration for natural laminar flow technology, under Airbus leadership.
The activities included in this project proposal aim to support the main development directions of the European project:
– Conception and design of the fuselage structure;
– The resistance calculation, laboratory testing, technical solutions validation;
– Elaboration of the technological documentation and manufacturing process tracking;
– Elaboration of the necessary documents for the Flight Approval Demonstrator.
INCAS will use its own facilities and the human research resource to achieve a demonstrator product at current technologies level, in line with the regulatory and project requirements. The Demonstrator Helicopter is intended to be the development of a new airframe configuration with superior quality to the existing ones. Also, the project opens a technological door way to further developments, offering a new dimension of rotorcraft.
INCAS will ensure the fuselage integration systems and equipment as well as the interfacing with the other structural elements: rear fuselage, wings, landing gear, etc.

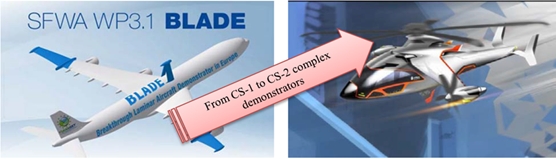
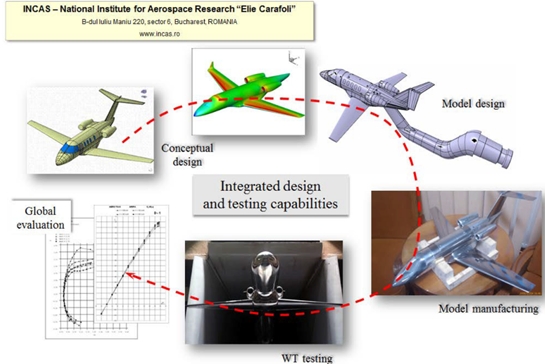
Romanian Partner
Within the European partnership, INCAS main objective is to make usage of the unique capabilities existing at the consortium level for design, manufacturing and testing of the fuselage for LifeRCraft Demonstrator in the Clean Sky 2 JTI.
The Manufacturing, testing and permit to fly support of the Demonstrator are carried out in collaboration with the industrial partner ROMAERO S.A.
The activities needed for developing and manufacturing the Fuselage of the LifeRCraft Demonstrator, as part of the Fast Rotorcraft IADP Clean Sky 2, are organized on the following work packages:
WP 0. Project Management
WP 1. Airframe Advanced Design
WP 2. Fuselage Manufacturing
WP 3. Permit-to-Fly
WP 4. Fuselage Testing
WP 0. Project Management
The work package WP0 is dedicated to project management and involve four tasks:
the overall project management
the dissemination and exploitation
the monitoring of technologies and configuration management
the development and the risk assessment and mitigation.
WP 1. Airframe Advanced Design
The design phase, has the following main requirements:
design and manufacturing of the fuselage based on the specifications provided by AIRBUS Helicopters – AH, in particular with regard to the weight that should not exceed 650 kg. The mechanism to achieve this goal is based on the Configuration Management activity, from WP0. It is a combined interaction with WP1 and WP2, where the configuration is monitored so that the global weight stays in the target.
analyzing the technical and economic aspects, particular designing of the components, of the processes, or other design features using specialized programs such as CATIA in order to ensure consistency of all subsystems.
providing technical and technological proposals for design and related manufacturing, in line with the CS2 program objectives.
WP 2. Fuselage Manufacturing
The manufacturing phase, is a specific manufacturing activity, based on the selected technologies in WP1, using capabilities available at the industrial partner:
INCAS will provide the necessary substantiation elements, descriptive documents, critical parts identification, complete stress analysis, failure analysis, fatigue calculations, test results, …) and documents in order to strongly and efficiently support this activity which is crucial for the success of the CS2 demonstrator.
the full structural integration of the fuselage.
WP 3. Permit-to-Fly
This Work Package is performed in close cooperation with AH. INCAS will contribute to the AH activities to obtain a permit to fly and will deliver:
Substantiation documentation for stress/fatigue/dynamic, vibration tests and bird strike analysis (if requested)
Documentation for flightworthiness according to a flight condition approval plan
Tests reports(entire test-pyramid)
Quality documentation for the delivered structural elements
Quality methods substantiation documentation
General Behavior of the fuselage (rigidity, deflection, etc.…)
Description of applied manufacturing processes.
In this phase INCAS will also include the tests to be performed in the program at the components’ level (or sub-components) in order to meet the requirements for permit to fly.
WP 4. Fuselage Testing
This WP will testing activities to be performed in RoRCraft project, aimed to validate the fuselage design and manufacturing technologies used.
providing the necessary information that lead to design improvement as well as identification of possible problems.
periodic verification of flight tests together with the industrial partners ROMAERO and AIRBUS Helicopters Germany.
providing the technical support to prevent the problems that may occur during the testing.
All activities are based on a Test Plan to be generated by the consortium, under INCAS leadership. This Test Plan will be approved by AIRBUS Helicopters and will include 2 major phases:
a. Ground integration tests
Tests will be performed in this phase to verify the satisfactory behavior of the fuselage integrated with other aircraft components. The goals is to support the substantiation process, to demonstrate the achieved level of safety and to get the necessary data for analyzing the forecasted tests results. The delivered articles will incorporate the necessary test instrumentation;
b. Flight tests to demonstrate the successful achievement of the CS2-project objectives.
This is the major challenge in LifeRCraft demonstration program. RoRCraft project will contribute by delivering the fuselage for this phase. The delivered article will incorporate the necessary flight test instrumentation, to de defined in the project.
The management structure consist of three level:
Level I. Operative level: Partners, task and WP leaders do the communication and decision making at WP levels.
Level II. Executive level: Project Coordinator and Steering Committee. The steering committee is the decision making body, gathering all parties including coordinator.
Level III. Strategic level: The communication and decision making is done between Partner Project Management and the ITD Partner/Leader.
These three levels will operate during the project’s lifetime whereas the coordinator is responsible for supervising all of the communication flows between the three levels.
Partners
The Clean Sky 2 Joint Undertaking (the”JU”), represented by Executive Director, Eric Dautriat,
of the one part, Airbus Helicopters, represented by Guillaume Faury, Chief Executive Officer (‘the coordinator‘), (‘Beneficiary no 1’)
and the following other beneficiaries, which together form the FRC IADP Consortium:
Organisation
1 – Airbus Helicopters sas
1a – Airbus Helicopters Deutschland
1b – Airbus Helicopters Polska
2 – Leonardo S.p.A.
2a – Wytwornia Sprzetu Komunikacyjnego PZL Swidnik
3 – Leonardo MW Ltd.
4 – National Institute for Aerospace Research “Elie Carafoli
6 – GE AVIO Srl
6a – GE Deutschland Holding GmbH
6b – GE Company Polska
6c – Avio Polska Sp.z.o.o
7 – Romaero S.A.
8 – Protom Group S.pA
9 – Triumph Actuation Systems – UK Ltd
10 – Latelec
11 – Centro Italiano Ricerche Aerospaziali SCPA
12 – Magnaghi Aeronautica
13 – Techno System Development srl
14 – Centre Composite LV
15 – M&S ENGINEERING Sk s. r. o.
Denumire | Data | Actualizări | Document |
---|---|---|---|
Mission for Clean Sky 2 | 2021 | 2015-11-01 | descarcă |
Clean Sky 2 LifeRCraft, at the end of the first official milestone | 2021 | 2016-11-01 | descarcă |
INCAS research work on the Clean Sky 2, High-Speed Compound Helicopter Demonstrator in 2017 | 2021 | 2017-11-01 | descarcă |
The Clean Sky 2 Hight Speed Helicopter model roll out at Paris International Airshow 2017 | 2021 | 2017-11-01 | descarcă |